Composites Engineering Handbook (Materials Engineering) P.K. Mallick on Amazon.com.FREE. shipping on qualifying offers. Offers information on the fundamental principles, processes, methods and procedures related to fibre-reinforced composites. Civil Engineering is responsible for projects that enhance the overall quality of life. Civil engineers design, construct, manage, operate and maintain the infrastructure that supports modern society including buildings, bridges, roads and highways, tunnels, airfields, dams, ports and harbours, railways, new mines, water supply and sewerage schemes, irrigation systems and flood mitigation works. Civil Engineering Books Collection. Builder’s Foundation Handbook - Hazardous waste land disposal. 3d Fibre Reinforced Polymer Composites, 4.9MB DOWNLOAD 26.
Table of Contents
Introduction - definitions, classifications and applications. Part 1 Constituents: fibres, fabrics and fillers; matrix resins and fibre/matrix adhesion. Part 2 Mechanics: micromechanics; mechanics of laminated structures; mechanics of woven fabric composites; fracture and damage mechanics in laminated composites. Part 3 Processing: processing for laminated structures; press moulding processes; filament winding; the pultrusion process for continuous automated manufacture of engineered composite profiles; processing of thermoplastic matrix composites; processing of particle-reinforced metal matrix composites; joining and repair of aircraft composite structures; machining of composite materials. Part 4 Properties and performance: laminated polymer matrix composites; random fibre composites; selection guidelines for metal matrix composites; ceramic matrix composites; cement matrix composites. Part 5 Testing: mechanical property measurements; nondestructive tests. Part 6 Engineering with composite materials: design methodology and practices; materials selection, preliminary design and sizing for composite laminates; design guidelines for laminated composites. HomeAdvanced Materials ResearchAdvanced Engineering MaterialsTechnological Properties of Poplar Particle/Waste...
Abstract:
The hot-pressing technology for the poplar particle /waste rubber powder composites was studied using the poplar particle and waste rubber powder as raw materials. Effects of waste rubber powder content, hot-pressing time, hot-pressing temperature, resin content and board density were analyzed. The hot-pressing technology was better than molding technology. The optimal technological parameters of hot-pressing technology were obtained as board density0.8g/cm³, resin content3%, hot-pressing temperature160°C, hot-pressing time 7min , waste rubber powder content 30%. The testing results showed that the mechanical performances of the poplar particle /waste rubber powder composites made by the hot-pressing technology could achieve the Chinese National Standard for particle board.
Jianmin Zeng, Taosen Li, Shaojian Ma, Zhengyi Jiang and Daoguo Yang
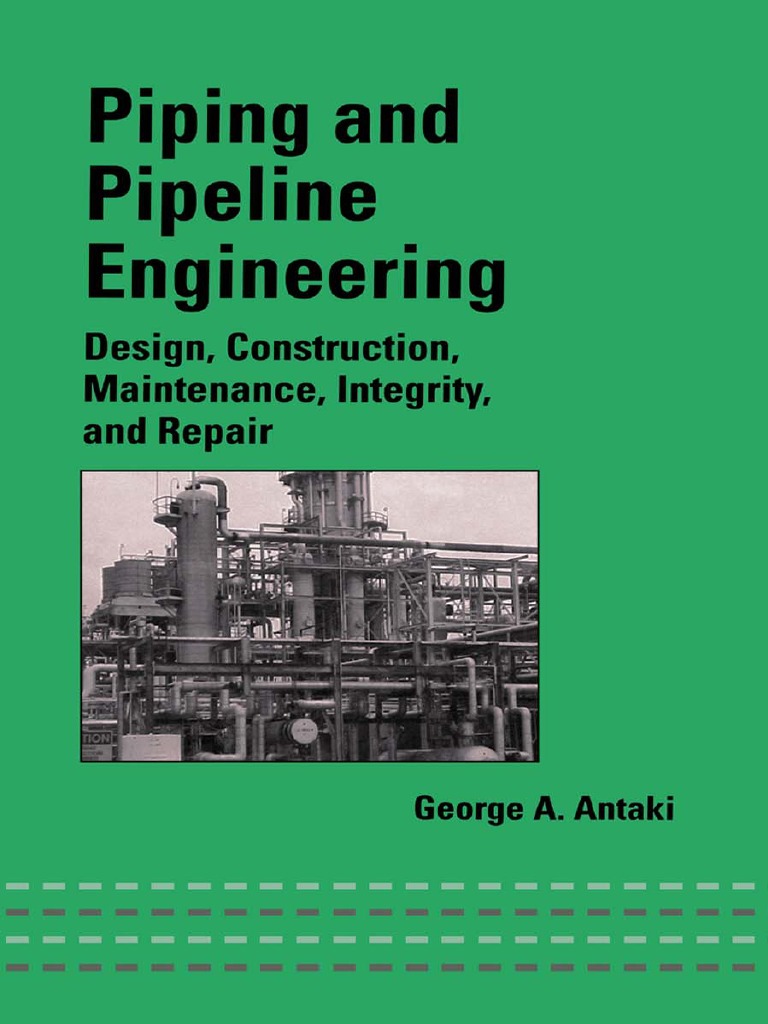
S. Y. Xin et al., 'Technological Properties of Poplar Particle/Waste Rubber Powder Composites', Advanced Materials Research, Vols. 194-196, pp. 602-605, 2011
Composite, Hot-Pressing Technology, Poplar Particle, Waste Rubber Powder
Free Hazardous Waste Disposal
[1] Anonymous, 2007. For Immediate Release: European Union Recycle Tire Test Results Announced. CBp Carbon Industries Inc., Bratislava, Slovakia, 2p.
[2] Wu, J.U.; Vallabhapuram, R. Hazardous Waste Management Handbook; PTR Prentice Hall: Upper Saddle River, NJ, (1994).
[3] Jun, Z, Wang, X., Chang, J., Zheng, K., 2008. Bioresource Technology 99, 2384-2391.
Local Hazardous Waste Disposal Sites
[4] Fu, Z., 2003. Publish House of Chemistry Industry, Beijing.
[5] Gu J. Y, Gao Z.H. Journal of Forestry Research 2002 (13): 74-76.
[6] Han S., Yang D.J., Kim, Young K.L. Bioresource Technology, 2004, (95): 61-65.
List Of Hazardous Waste
[7] Pizzi A. Wood Adhesive Chemistry & Technology [M]. Marcel Dekker. NewYork: 1983. 295.
Abstract: Titanium metal matrix composites were produced. The powder metallurgy route applied was a conventional route consisting of blending titanium matrix powder with different percentages of various titanium compounds, as reinforcement particles, followed by cold compaction in a uniaxial press with a floating matrix and a sintering process in a vacuum furnace. This work studied the different interactions between the titanium matrix and the various titanium compounds added. To evaluate these interactions microscopic techniques are used principally, optical and electronic microscopy, with EDX techniques. By microstructural analysis the reactivity between reinforcement and matrix particles was investigated, and any new phases that formed during the sintering process were evaluated. In addition, microhardness test were conducted to study the mechanical properties associated with the new phases, and to evaluate the relative strength or weakness of the interfacial zones.
817
Abstract: Authors discussed the effect of organic and inorganic dyes on the properties of wood fiber/HDPE (WF/HDPE) composite. Iron oxide red, iron oxide yellow, iron blue, everbright fast red, permanent yellow, and phthalocyanine were used. Test results indicated that organic dyes provided brighter color and higher flexible properties to WF/HDPE composite than inorganic dyes. However, when exposed to UV weathering, WF/HDPE composites with inorganic dyes were more durability than those with organic dyes.
2293

Abstract: We investigated the effects of amount of antioxidants variability on selected mechanical and physical properties of wood plastic composites. Recycled high density polyethylene (rHDPE) and natural fibers were compounded into pellets by compounder, then the pellets were extruded using co-rotating twin-screw extruder and test specimens were prepared by hot and cold press process. From the study, samples with 0.5 wt% of antioxidants produce the highest strength and elasticity of composites. The effect of antioxidants presence on water uptake is minimal.
151
Abstract: Mo-based composites with Al2O3 particles were developed in order to enhance the wear resistance of molybdenum alloys. Using Al2O3 power and pure Mo power as raw materials, the Molybdenum powders mixed with Al2O3 particles were prepared using planetary ball mill. And then the Mo-based composites with 3-10vol.% Alumina were prepared by compaction and sintering at 1840°C. The morphology of the Molybdenum powder and microstructure of the composites were analyzed by SEM and XRD. The micro-hardness, density and wear property of composites were researched. The results show that the microstructure of composites is composed of α-Al2O3 particles and Molybdenum matrix. With the increase of Alumina content, the microhardness of Molybdenum matrix increases, and the density first increases and then decreases. The friction coefficient of composite is scarcely affected by the alumina content. While the wear resistance of the composites rises with the increase of Alumina content. The wear failure is caused by abrasive wear characterized by obvious plow furrow and abrasive dust on the worn surface.
467
Abstract: Composites made from phenolic resin are filled with conductive filler mixtures containing copper powders, natural graphite powders and carbon fibers. They are fabricated by compression molding technique. The density, electrical conductivity and hardness of composite are analyzed to determine the influence of copper particle size on the physical, electrical and mechanical properties of composite. It is found that there is a marked dependence of the electrical conductivity and hardness on copper particle size. The hardness decreases with the decreasing of copper particle size. However the electrical conductivity increases with the decreasing of copper particle size. The decreasing of copper particle size from 75 µm to 48 µm promotes a considerable increase in electrical conductivity by about 427%. The increased continuous conductive metal networks could be the main reason for the increasing of electrical conductivity as copper particle size decreases. The results also show that composites containing copper particles of different sizes have the nearly same density.
120